Offset, Digital & Flexography: Printing Approaches Contrasted
The physical understanding of product packaging involves crucial decisions relating to printing methodologies. While useful item style and engaging branding are paramount, the picked printing process dramatically affects the final aesthetic, price, and and scalability.
Intro
The physical understanding of product packaging involves crucial decisions relating to printing methodologies. While useful item style and engaging branding are paramount, the picked printing process dramatically affects the final aesthetic, price, and and scalability. Technical innovations have actually significantly broadened the selection of readily available printing methods. This diversity encourages businesses to select an approach that aligns precisely with their financial constraints, production volume requirements, and wanted print quality. This analysis provides a relative assessment of three core printing strategies prevalent in the packaging sector: Lithography (commonly known as Offset Printing), Flexography, and Digital Printing. Understanding the operational principles, advantages, and constraints of each is crucial for enhancing personalized bundle production.
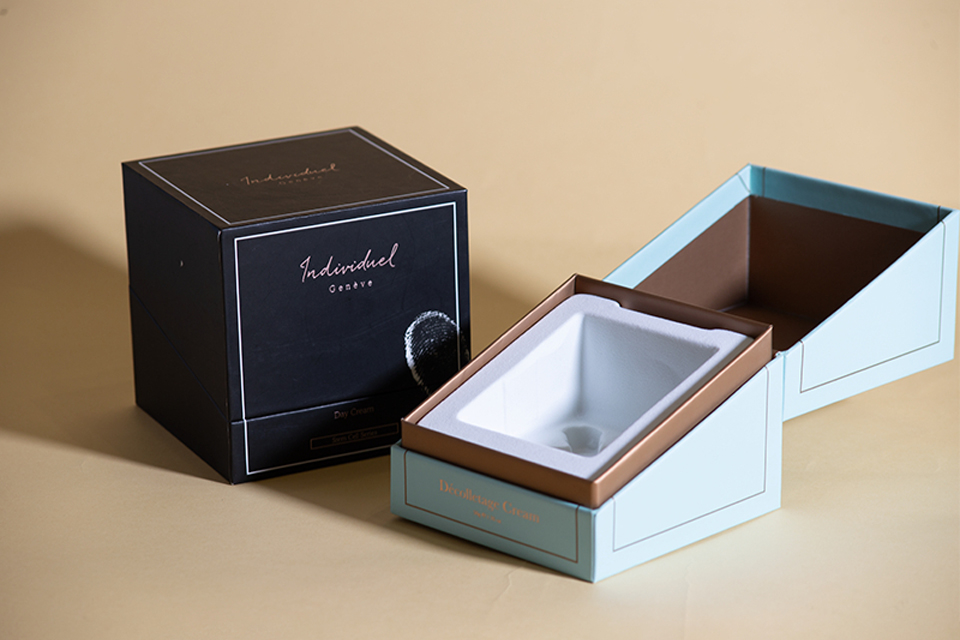
Lithography (Offset Printing): Principles and Applications
Lithography, much more regularly described Offset Printing, operates the essential principle that oil and water do not mix. In this multi-step procedure, an image is first moved (countered) from a steel printing plate to a rubber blanket. Consequently, the rubber blanket transfers the inked photo onto the printing substrate, typically paper or cardstock. For full-color printing making use of the CMYK (Cyan, Magenta, Yellow, Key/Black) color version, Offset Printing requires 4 distinct printing plates. Each plate represents one of the CMYK shades. This approach likewise expertly supports the Pantone Matching System (PMS) for exact area shade recreation and combinations thereof.
A crutial financial consideration in Offset Printing is that arrangement prices mainly connect with the number of unique art work layouts, not the amount of the same structural designs. As an example, creating 1000 systems for each of two different artwork styles incurs fees for two different plate-making and arrangement processes. On the other hand, publishing 2000 systems of a solitary style shows much more cost-efficient. This is because it gets rid of the need for plate changes throughout the print run. Offset Printing is renowned for its exceptional print high quality. It regularly supplies extraordinary color integrity, sharpness, and crisp information. Subsequently, industries commonly employ it for high-volume production of costs product packaging. In some areas, like the United States, quantity thresholds for affordable Offset Printing can be reasonably high (e.g., 5000 devices). Listed below such quantities, Digital Printing frequently presents a more viable alternative.
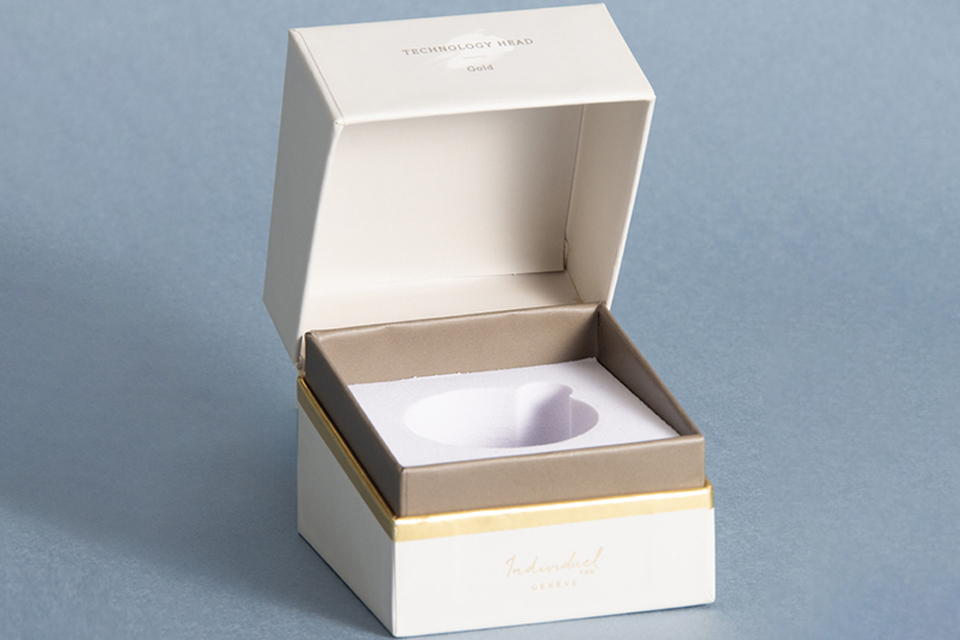
Flexography: A Direct-Transfer Printing Method
Flexography, commonly abbreviated to “Flexo,” shares some conceptual similarities with Offset Printing but differs substantially in its ink transfer system. In Flexography, versatile photopolymer printing layers transfer ink straight onto the substratum. This substrate can vary from paper and corrugated board to plastics and metal movies. One can visualize htis process as a sophisticated type of marking. The inked, increased picture on tjhe adaptable plate straight inscribes onto the product packaging product. Similar to Offset Printing, if utilizing the CMYK shade system, Flexography calls for a different plate for each color.
Flexography is well-suited for large-volume print runs. It typically supplies reduced per-unit prices contrasted to Offset PRinting for substantial manufacturing. This cost-efficiency comes from the straight ink transfer, removing the intermediate covering cylinder. Nonetheless, the print top quality attained with Flexography, while continuously enhancing, typically does not match the fine information and halftone subtlety of Offset Printing. Reproducing detailed designs and complicated multi-color slopes can offer challenges. Industries frequently utilize Flexography for printing on flexible product packaging, such as plastic pouches and food wrappers, as well as corrugated boxes where high-resolution graphics are not the primary issue.
Digital Printing: Plate-Free, On-Demand Manufacturing
Digital Printing represents a standard shift from conventional plate-based methods like Offset Printing and Flexography. It directly transfers electronic photo documents to the printer, which after taht applies ink or printer toner to the substrate. Common desktop printers exhibit fundamental Digital Printing. Commercial-grade digital presses, designed for larger amounts (e.g., 50-100+ systems), may utilize fluid ink or innovative toner modern technologies. A main advantage of Digital Printing is the very little configuration called for. Layouts prepared on a computer can be printed nearly instantly. This characteristic makes Digital Printing exceptionally fit for short print runs, print-on-demand applications, and jobs calling for variable information printing (e.g., one-of-a-kind codes or tailored messages on each plan).
In Digital Printing, setting you back models usually associate with tje variety of printed things (structures) rather than the number of special styles, as no physical plates need transforming. This adaptability makes it affordable for creating several layout variants in reduced quantities. Nevertheless, Digital Printing additionally presents specific restrictions. The cost of toners and consumables can make it expensive for very large print quantities. While color precision and quality have enhanced drastically, attaining specfic PMS color matching can be a lot more tough than with Offset Printing. Publishing large strong blocks of shade might sometimes lead to tonal variances or banding. Result top quality can somtimes appear much less sharp or slightly pixelated contrasted to the clarity of Offset PRinting, especially for elaborate information.
Comprehending Color Gamut and Resolution Capabilities
A critical technological distinction among Offset Printing, Flexography, and Digital Printing depends on their color recreation capacities and achievable resolution. Offset Printing usually boasts the widest color range, especially when including PMS spot shades. This allows for highly exact and dynamic shade matching, critical for brand uniformity. IT additionally excels at reproducing fine lines, tiny text, and detailed photographic images iwth high fidelity as a result of its accurate ink control and plate technology.
Flexography, while capable of generating high quality shade, commonly had a more limited shade range and reduced resolution compared to offset. Nonetheless, improvements in anilox roller technology, plate materials, and inks (HD Flexo) have actually dramatically narrowed this space. It currently supplies much-improved visuals top quality, ideal for a more comprehensive range of packaging applications.
Digital Printing modern technology varies commonly. Premium digital presses can attain outstanding color precision and resolution, coming close to countered top quality for numerous applications. Nonetheless, the uniformity of color across a future and the capacity to perfectly match specific PMS shades can still be a lot more reliably attained with Offset Printing. The resolution of Digital Printing depends on the certain printer modern technology (e.g., dots per inch or DPI), and while generally great, it could not constantly match the ultra-fine information possible with top notch offset plates. These distinctions directly influence the aesthetic impact and perceived high quality of the last published packaging.
Arising Hybrid Printing Solutions
The printing industry is seeing the surge of hybrid printing presses. These sophisticated systems strategically integrate the strengths of different printing technologies. For instance, a hybrid press may integrate Digital Printing heads onto a Flexography or Offset Printing line. This permits the cost-efficient printing of static, high-volume components making use of the conventional approach, while the electronic devices handle variable information, short-run customizations, or special effects. This strategy supplies unmatched versatility. It allows mass modification, enhances security features via one-of-a-kind identifiers, and maximizes manufacturing workflows. Crossbreed solutions stand for a significant action towards bridging the gap between the high-volume effeciency of traditional methods like Offset Printing and Flexography, and the dexterous, variable information capacities of Digital Printing. This convergence resolves the progressing market demand for both individualized and economically generated product packaging.
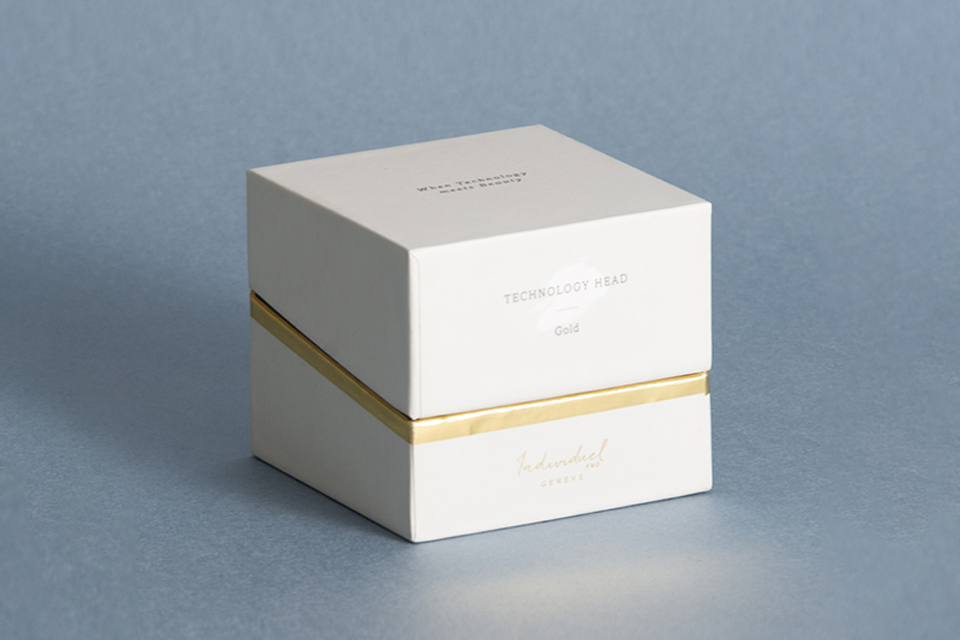
FInal thought
The selection of an optimal printing approach– be it Offset Printing, Flexography, or Digital Printing– is a diverse decision. There is no widely exceptional method; each deals distinct benefits tailored to specific task needs. Offset Printing masters high-volume situations demanding costs print quality and specific color integrity. Flexography supplies a cost-efficient service for massive manufacturing, particularly on diverse substratums, though with commonly some concession on complex detail. Digital Printing uses unparalleled flexibility for short runs, fast prototyping, andd variable data applications. Organizations have to meticulously examine their volume needs, financial allocations, layout complexity, substratum options, and desired quality standards. A comprehensive understanding of these core printing technologies equips notified decision-making. This eventually leads to product packaging that efficiently connects brand worth and engages customers.