Managing Color Deviation in Packaging Box Production
The proliferation of customized product packaging box services equips brands dramatically. Brand owners progressively seek bespoke product packaging box manufacturers.
Introduction
The proliferation of customized product packaging box services equips brands dramatically. Brand owners progressively seek bespoke product packaging box manufacturers. They currently look at finer production details with better attention. Amongst these vital components, shade uniformity in packaging box production needs meticulous oversight. This document deals with the idea of practical shade distinction. It discovers its effects throughout the packaging box producing lifecycle. Accomplishing absolute colorful replication between layout proofs and final product packaging box units continues to be a technological unfeasibility. Proofing acts as a crucial reference criterion, not an ensured ideal match. Makers of packaging box products need to plainly communicate this. They should specify that sample box shades are indicative. The last outcome’s shade eventually aligns with the physical production run. This openness helps preempt possible disagreements. Nonetheless, any color variation need to fall within an objectively affordable and industry-accepted tolerance range. We will certainly take a look at the variables adding to these shade changes and approaches for their effective administration.
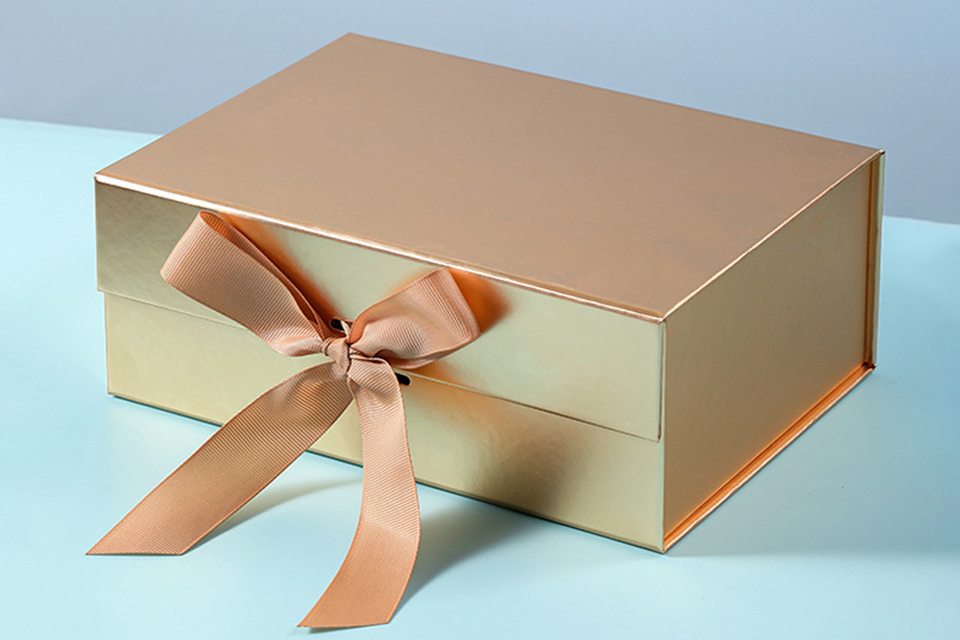
The Inevitability of Color Variant in Product Packaging Box Manufacturing
A particular degree of inconsistency in between the desired style color and the real shade of a finished packaging box is an integral facet of the printing and production procedure. This sensation is medically specific. Occasionally, client mental assumptions contribute to regarded disparities. Clients may really feel that the final product packaging box color does not flawlessly align with their preliminary mental image or the supplied proof. They might then view this as harmful to their firm’s picture or even influencing future orders. On the other hand, the packaging box producer usually checks out the observed shade variance as appropriate. They consider it a regular, inescapable shade difference within well-known industry criteria. It is critical to recognize that this discrepancy exists objectively. One can not completely associate obligation for minor shifts to the custom packaging box maker. The manufacturer’s role entails proactively minimizing this error to the lowest achievable level. Total elimination of color difference, nevertheless, continues to be beyond present technical abilities in mass packaging box production. Several complicated variables interact during production, making excellent color matching across various substrates and print runs remarkably challenging.
Technical Factors Affecting Shade in Product Packaging Box Manufacturing
A number of interconnected technological variables inherently contribute to tint variations throughout product packaging box manufacturing. The substrate, or the product of the product packaging box itself (e.g., numerous paperboards, corrugated products, plastics), plays a basic function. Different substratums possess special surface area attributes, consisting of color, illumination, absorbency, and texture. These qualities straight influence just how ink shows up as soon as used. For example, an extremely absorbing, uncoated paper supply will make shades differently than a smooth, coated, intense white board. Ink solution is another essential variable. Printing inks contain pigments or dyes suspended in an automobile. The specific pigments, their focus, and the car’s buildings impact the final color. Different ink sets, even from the same supplier, can show minor variations. The printing process itself introduces variables. Offset lithography, flexography, electronic printing, and display printing each have distinctive mechanisms for moving ink to the packaging box substrate. Factors like ink film thickness, dot gain (the spreading of ink dots), trapping (how shades overprint), and drying out or healing approaches considerably affect the viewed color. Ecological problems, such as ambient temerature and humidity in the print center, can also affect ink actions and substratum homes, subtly affecting the final shade of the product packaging box .
The Function of Color Proofs and Samples in Handling Assumptions
Color evidence and physical samples are indispensable tools in the product packaging box personalization workflow. They serve as crucial communication help between the customer and the producer. However, their function and limitations need clear understanding. A digital proof, seen on a monitor, provides an initial visual representation. Yet, display calibrations differ extensively, making on-screen shade subjective. An agreement evidence, frequently a premium inkjet or press proof, offers an extra exact forecaster of the final packaging box color. Makers create these proofs utilizing shade management systems adjusted to their printing presses. However, an agreement proof stands for a perfect scenario, typically on a certain proofing stock. It might not flawlessly reproduce the outcome on the real packaging box substratum under automation problems. Physical pre-production examples of the product packaging box , printed on the final product with the intended inks and procedures, supply the closest estimation. These samples enable clients to examine color, surface, and building prior to committing to a full production run. Manufacturers ought to plainly clarify that even these samples stand for a target. Small variants in the full run due to normal procedure irregularity are still possible. Efficient communication relating to the function and integral restrictions of different proofing phases for the packaging box is vital. It aids set realistic expectations and promotes a collaborative strategy to shade administration.
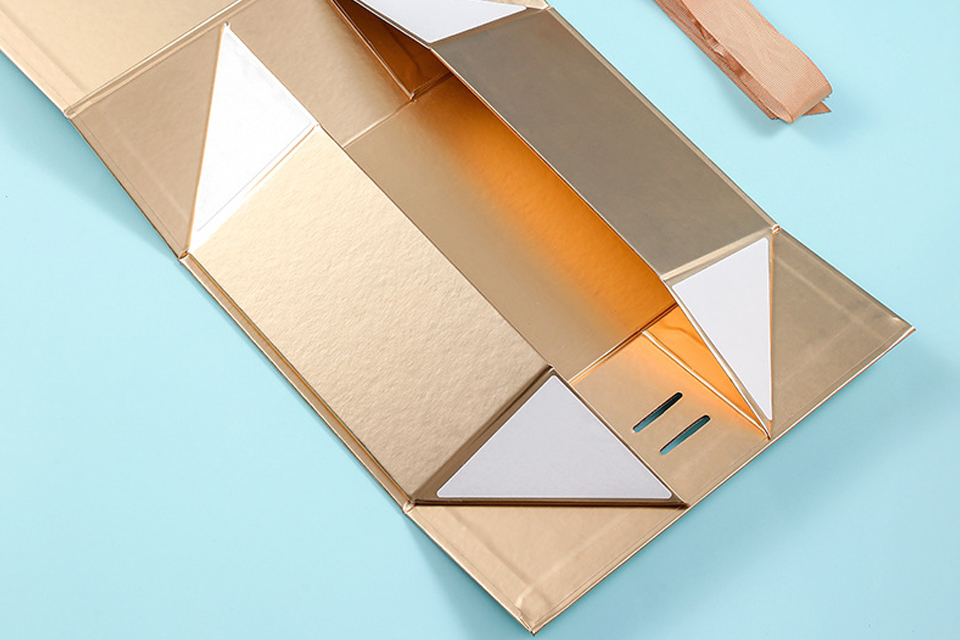
Standardization and Control of Shade Variation in Packaging BOxes
While eliminating color difference in packaging box production is not viable, makers utilize extensive standardization and control measures to take care of and reduce it. Sophisticated shade administration systems (CMS) form the backbone of this effort. A CMS includes calibrating all gadgets in the operations– from design monitors and proofers to printing presses. It uses standard shade profiles (e.g., ICC accounts) to ensure regular shade analysis throughout various tools. Spectrophotometers are important instruments in this this process. These devices precisely gauge shade, providing objective colorimetric infomation (e.g., L a b values). Suppliers make use of spectrophotometers to measure shade on evidence, ink drawdowns, and manufacturing examples of the product packaging box . They compare these dimensions against established shade criteria or approved master examples. The difference in between 2 color dimensions is frequently revealed as Delta E (ΔE). A reduced Delta E value indicates a more detailed match. Market requirements and client specifications usually define appropriate DElta E tolerances for a packaging box . By consistently keeping an eye on shade with such tools, printers can determine and fix discrepancies proactively. They can adjust ink thickness, press setups, or other variables to maintain the packaging box color within the agreed-upon range. This data-driven approach relocates color evaluation from subjective visual perception to objective, quantifiable control, making sure greater consistency for the final * packaging box .
Custom packaging box suppliers prioritize durable shade difference administration. They identify its critical role in the general success of any type of product packaging customization task. This emphasis originates from comprehending that color straight impacts brand name perception and product allure. As a result, their operational procedures naturally intend to stay clear of recognizable shade disparities anywhere possible. For those color variants that contemporary printing modern technology can not completely prevent, makers concentrate intensely on minimizing these mistakes to the absolute minimum possible. This commitment entails a multi-pronged method. It consists of thorough calibration of printing devices, careful selection and control of basic materials like inks and substratums, and extensive quality assurance checks at numerous stages of product packaging box manufacturing. Experienced press operators additionally play a vital part. They use their competence to make great adjustments during the print go to preserve shade uniformity. The overarching goal is always to produce top notch packaging box devices that align as carefully as feasible with the customer’s accepted layout specs and promote thge stability of their brand name.
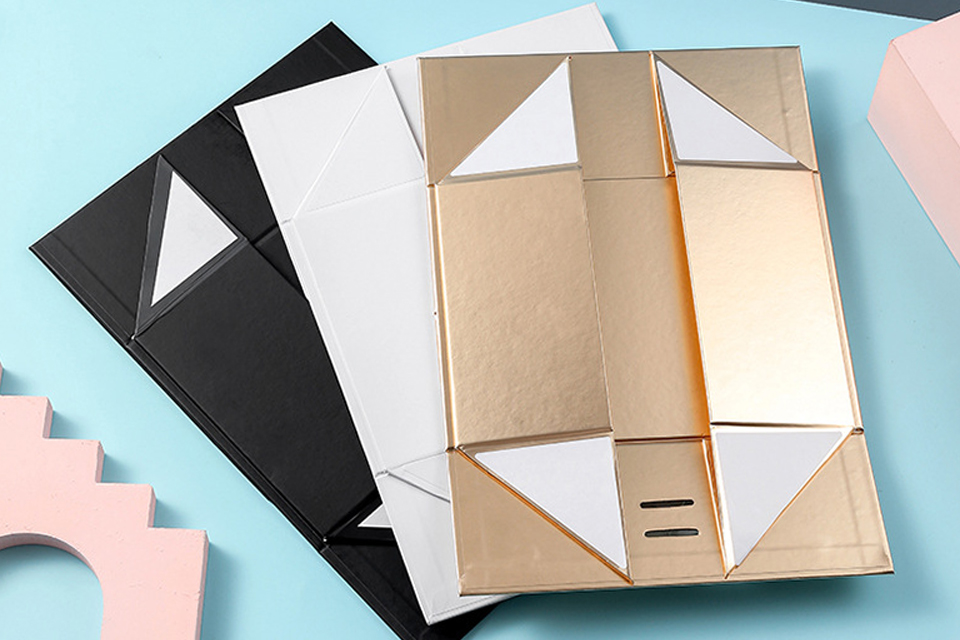
Verdict
In conclusion, accomplishing excellent, outright shade uniformity in between design intent and the last produced product packaging box offers a continuous technological challenge. Some level of shade variant is an unbiased truth in the complicated printing and manufacturing setting. Brand name owners and and packaging box makers need to acknowledge this. Open up communication, clear definitions of appropriate resistances, and the proper use of color evidence and samples are important for handling expectations and stopping conflicts. Reliable packaging box suppliers spend heavily in shade monitoring modern technologies, standardized procedures, and competent employees. They do this to decrease color inconsistencies efficiently. Their objective is to guarantee that any kind of variance continues to be within a reasonable, industry-accepted range. While customers must comprehend the inherent limitations, producers bear the duty of using finest methods to control color meticulously. This thorough stradegy inevitably supplies a premium packaging box that precisely reflects the brand’s picture and meets the practical and visual demands of the item. The pursuit of marginal color difference remains a vital efficiency sign for quality in product packaging box producing.