Avoiding Yellowing in White Cardboard Packaging Boxes
White cardboard serves as a premier substrate for building premium packaging boxes . Its inherently intense and tidy surface area provides a phenomenal canvas for dynamic branding and innovative product presentation.
Introduction
White cardboard serves as a premier substrate for building premium packaging boxes . Its inherently intense and tidy surface area provides a phenomenal canvas for dynamic branding and innovative product presentation. This aesthetic quality often conveys a feeling of premium value and health to customers. Nonetheless, a persistent difficulty intimidates this beautiful appearance: the phenomenon of yellowing. This progressive staining can considerably diminish the visual appeal of product packaging boxes . Consequently, it may adversely influence brand perception and deteriorate consumer trust. Recognizing the complex chemical systems thgat drive this yellowing process is necessary. Executing efficient, scientifically-grounded preventative procedures is therefore critical for producers and brands. These entities rely upon aesthetically superior product packaging boxes to represent their items. This short article thoroughly takes a look at the clinical principles governing cardboard yellowing. It better lays out innovative, workable methods to mitigate this pervasive problem. The goal is to make sure long-lasting color security and keep the visual stability of white cardboard product packaging boxes .
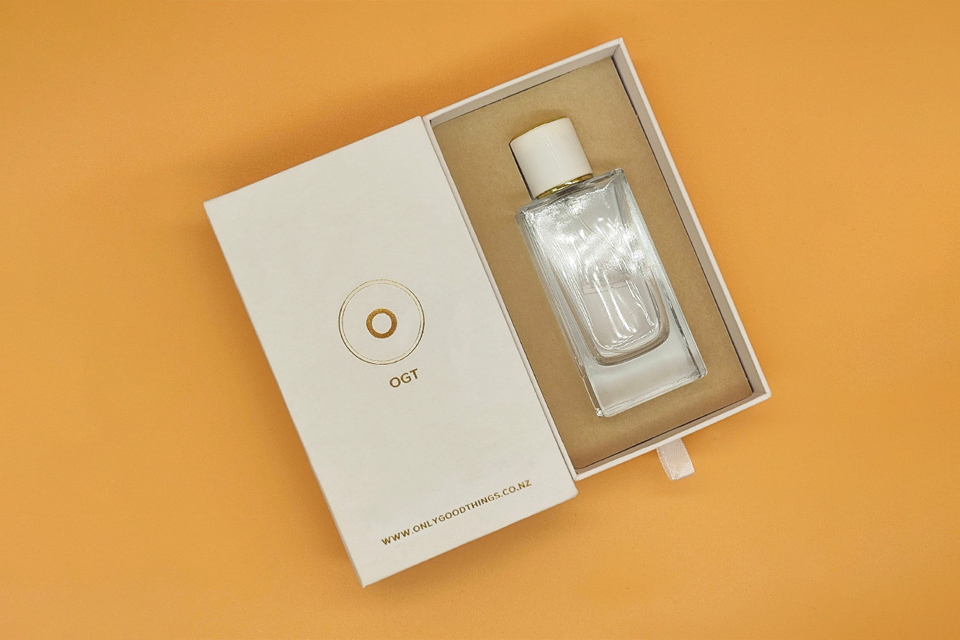
Refine Adjustment of Coated Base Paper for Product Packaging Boxes
Makers execute critical process modifications in covered base paper manufacturing to fight yellowing in product packaging boxes . A primary method involves the careful use pulp types. They focus on bleached chemical wood pulp for the important surface area layers of the paperboard. This specific pulp goes through substantial processing to get rid of the majority of lignin. Lignin is an all-natural timber polymer extremely susceptible to oxidation and photodegradation, which are primary chauffeurs of yellowing. By boosting the amount of this low-lignin surface area pulp, suppliers accomplish enhanced insurance coverage. This thickened surface area layer properly serves as a safety obstacle. It shields any type of hidden mechanical pulp, which inherently has a higher lignin percentage, from exterior derogatory elements like light and oxygen. Superior protection therefore directly lessens the danger of discoloration, protecting the aesthetic quality of the finished product packaging boxes .
Carrying Out Medium-Alkaline Sizing for Enhanced Security
Transitioning to a medium-alkaline sizing process is a keystone of yellowing avoidance for white product packaging boxes . This innovative technique considerably decreases the reliance on light weight aluminum sulfate (alum). Alum, utilized in standard acid sizing, can leave acidic deposits in the paper. These residues promote acid hydrolysis of cellulose fibers and increase lignin destruction, resulting in yellowing. The medium-alkaline process actively boosts tjhe base paper’s pH value. Comprehensive empirical research and industrial trials confirm that maintaining the surface layer’s pH between 6.5 and 8.0 is optimal. This slightly alkaline environment passivates many degradative chemical reactions. Papermakers must also meticulously control drying temperatures during manufacture. They should reduce operational drying temperatures to the lowest feasible point while still ensuring complete moisture removal and paperboard dryness. Furthermore, the efficient operation of cold cylinders, for both base paper and coated paper, is vital. These cylinders rapidly cool the paper web, quenching thermal reactions and stabilizing the sheet. These measures collectively contribute to a more stable paper, ideal for long-lasting white packaging boxes .
Strategic Application of Coloring Pigments in Packaging Boxes .
The judicious application of coloring pigments provides another layer of defense and aesthetic control for packaging boxes . Manufacturers use specific tinting pigments, usually blue or violet, to counteract any inherent yellowness in the pulp or coating. This process perceptually shifts the cardboard’s color towards a neutral or desirable bluish-white. A key objective is to maximize CIE whiteness, a standardized industry metric. This often allows for a reduction in the amount of Optical Brightening Agents (OBAs) or fluorescent brighteners. While OBAs enhance brightness, they can degrade under UV light and contribute to later yellowing. Manufacturers meticulously balance various chemical raw materials, including pigments, to achieve the target hue and whiteness for premium packaging boxes . To effectively reduce yellowing in coated white paper, the selection criteria for coloring pigments are stringent. The chosen pigments must demonstrate high light resistance (lightfastness), meaninng they do not fade or change color upon light exposure. They must also be easy to integrate into production. High-quality organic pigments generally offer superior performance in these aspects. Their chemical stability and lightfastness are typically ideal for demanding applications. Precise control over the pigment quantity is also critical. An excessively high concentration can paradoxically aggravate yellowing or lead to an undesirable color cast on the packaging boxes . Conversely, an insufficient amount will fail to achieve the required whiteness and masking of yellowness.
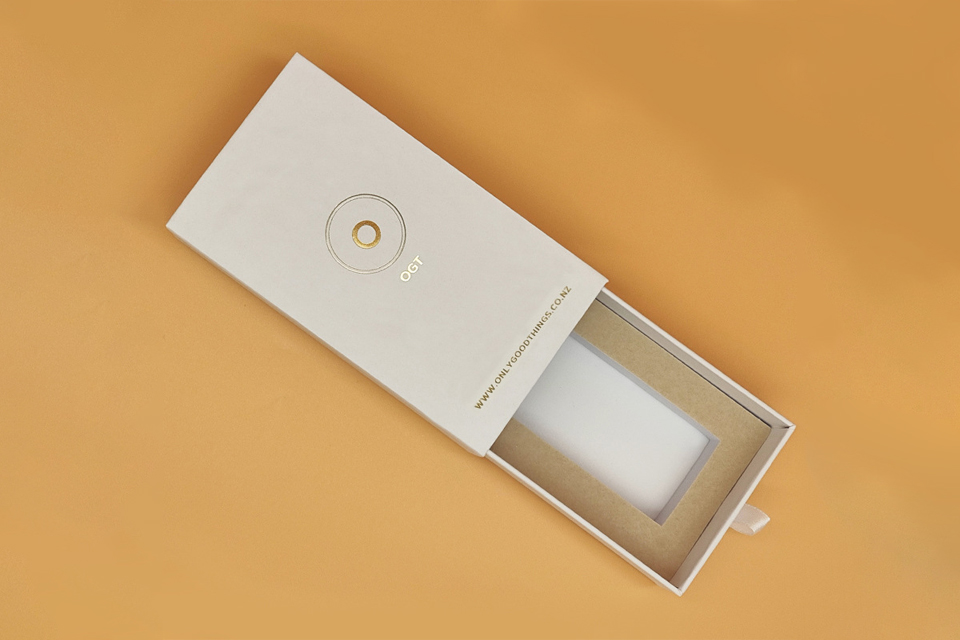
Selecting Advanced Chemical Additives for Protection
Modern paper chemistry offers novel chemical additives that significantly enhance yellowing resistance in materials for packaging boxes . Emerging research and practical applications highlight the efficacy of nano-silicon-based oxides when incorporated into coating formulations. These advanced nanomaterials possess unique molecular structures and an exceptionally high surface-area-to-volume ratio. This allows them to interact effectively within the coating matrix. Their mechanism for reducing yellowing likely involves a combination of UV light scattering, scavenging harmful free radicals, and forming a protective nanoscale barrier. Visual aging tests, which simulate accelerated degradation, demonstrate that coatings with these nano-oxides show markedly less increase in the chromaticity b value (a measure of yellowness). This indicates superior long-term color stability. Furthermore, thge incorporation of ultraviolet (UV) absorbers adn antioxidants offers additional protection. UV absorbers function like a molecular sunscreen. They preferentially absorb damaging UV radiation and dissipate it as harmless heat, shielding lignin and cellulose in the packaging boxes from photochemical degradation. Antioxidants, on the other hand, interrupt oxidative degradation pathways. They react with and neutralize highly reactive free radical species, which are precursors to chromophore (color-causing group) formation. These additives work synergistically to preserve the whiteness of * packaging boxes .
Crucial Environmental Controls for Packaging Boxes
The surrounding environment profoundly influences the color stability of white cardboard. Therefore, implementing crucial environmental controls during storage and display of packaging boxes is essential. Factors such as high ambient humidity, elevated temperatures, and prolonged exposure to direct sunlight or artificial UV-rich light sources significantly accelerate yellowing reactions. Both manufacturers of packaging boxes and end-users must actively manage these conditions. Storing finished packaging boxes in cool, dry, and dimly lit environments helps preserve their original whiteness. Shielding them from atmospheric pollutants, including nitrogen oxides (NOx) and sulfur dioxide (SO2) often found in urban or industrial air, also mitigates discoloration. These preventive handling adn storage practices are vital for maintaining the aesthetic integrity of high-value packaging boxes .
Addressing Ancillary Factors in Yellowing Prevention
Other factors also influence the yellowing of white cardboard for packaging boxes . Controlling the coating’s pH value is important; acidic coatings can reduce stability. Purifying coating water removes contaminants taht might catalyze yellowing. The choice of coating starch impacts color reversion potential. Maintaining correct final moisture content in the paperboard is also vital, as excess moisture speeds degradation. Careful packaging and storage of paperboard and finished packaging boxes are crucial. Addressing these aspects strengthens overall yellowing prevention for packaging boxes .
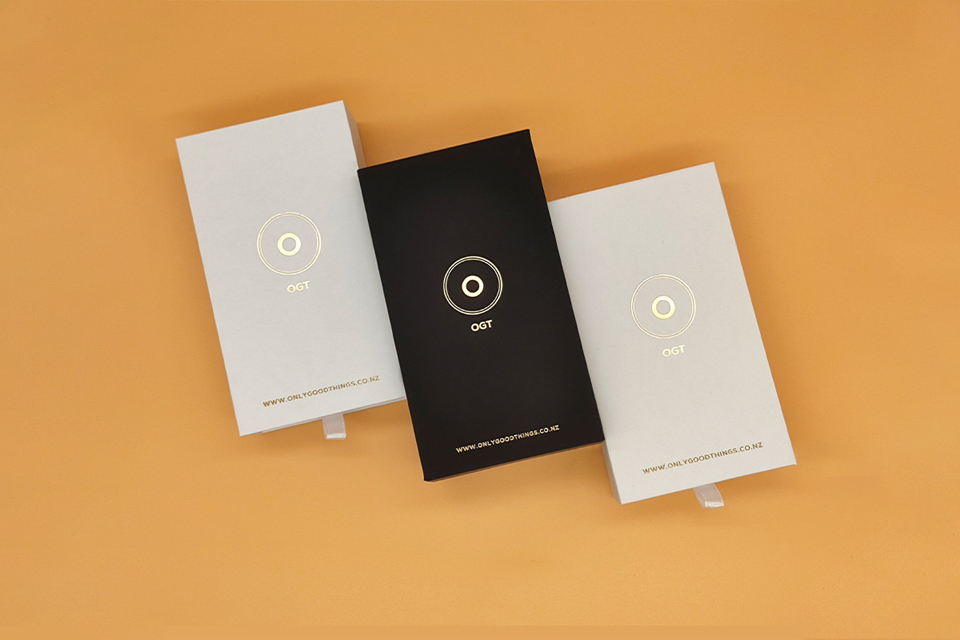
Conclusion
Successfully launching high-quality white cardboard packaging boxes necessitates a comprehensive strategy to prevent yellowing. BY adjusting base paper processes, implementing alkaline sizing, using appropriate pigments and advanced additives, and controlling environmental and ancillary factors, manufacturers can significantly enhance the color stability of their packaging boxes . These scientific and technological approaches ensure taht packaging boxes retain their pristine appearance, upholding brand image and consumer satisfaction. Proactive prevention is key to delivering superior and durable packaging boxes .