Comprehending Surface Area Problems: Product Packaging Box Bubbling Causes
Consumers regularly create instant judgments about product high quality. A product's outside discussion strongly affects these initial assumptions.
Intro
Consumers regularly create instant judgments about product high quality. A product’s outside discussion strongly affects these initial assumptions. THe visual and tactile qualities of product packaging boxes play a considerable function in this analysis. When product packaging boxes exhibit unwanted imperfections like gurgling, their regarded worth swiftly decreases. Buyers may link such defects with second-rate manufacturing. They might also presume reduced item top quality or an absence of brand interest to detail. This unfavorable impression can undermine brand name online reputation. It can also erode customer depend on, which is hard to rebuild. As a result, a detailed understanding of gurgling causes in packaging boxes is important for manufacturers. This article supplies an in-depth evaluation of variables leading to this common problem. We will explore physical andd chemical devices behind bubble delevopment. We will certainly alsot highlight preventative measures and quality assurance.
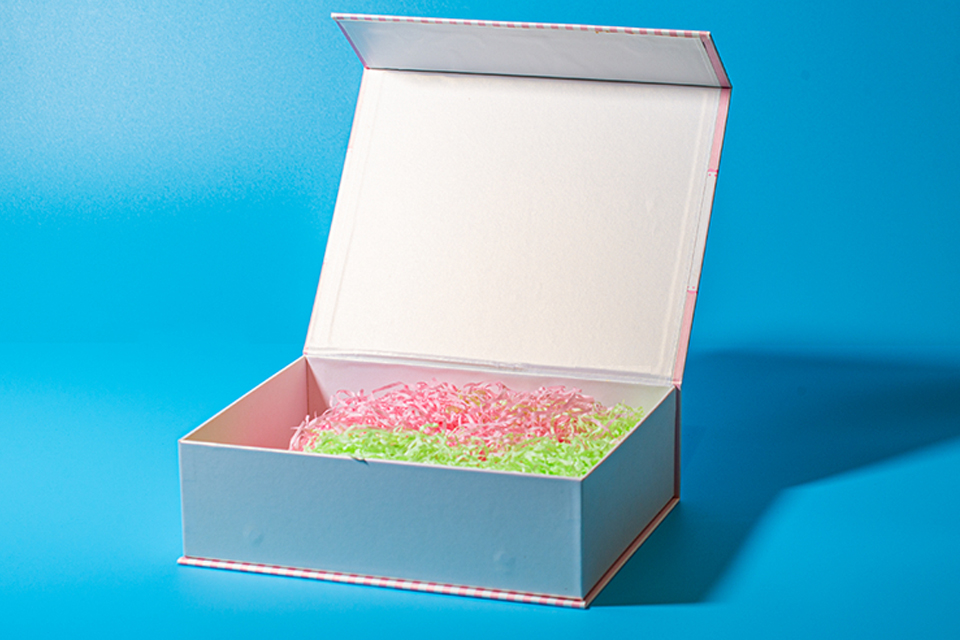
The Important Duty of Environmental Dampness Control
Paperboard functions as a foundational material for several product packaging boxes . This product has a remarkable hygroscopic nature. This property indicates it easily absorbs ambient wetness from its environments. It additionally releases moisture when the setting ends up being drier. Throughout periods of high ambient moisture, such as stormy seasons or in inadequately aerated storage space, cardboard’s interior moisture web content can raise dramatically. Warehouses storing these paper-based raw materials need to consequently carefully maintain controlled environmental conditions. If cardboard with extreme moisture continues to the lamination or gluing stage of packaging boxes production, considerable troubles can develop. Warmth used during adhesive treating, or pressure from laminating flooring rollers, can trigger this entraped dampness to swiftly vaporize. This stage change produces interior pressure. Additionally, differential expansion can happen. This takes place when the moist cardboard core expands at a different price than tjhe usually drier face product. Both mechanisms– evaporation and differential expansion– generate inner stress and anxieties in between layers. These stresses cause layer separation. This splitting up manifests as bubbles on the surface of finished product packaging boxes . Effective desiccation systems or detailed environment control are vital for resources honesty. They likewise prevent such moisture-induced issues.
Precision in Adhesive Application Machinery
The mechanical application of adhesive is a very precise procedure in making high quality packaging boxes . Small deviations from ideal settings in laminating or gluing machinery can straight add to appear problems. Wrong equipment calibration is a typical wrongdoer. Technicians should meticulously readjust essential criteria. These consist of regular stress by applicator rollers and accurate void settings between these rollers. Failure to preserve appropriate requirements causes a non-uniform adhesive film. Consequently, some locations of the face paper, or the core board of the packaging boxes , might receive adequate adhesive. However, various other sections may receive inadequate adhesive, or none in all. When these unevenly glued products are pressed together, unbonded sections create gaps. Air can become trapped within these spaces. Succeeding operations, like wrapping or last setting up stress, create these unglued areas to raise. This training manifests as visible bubbles on the product packaging boxes . Constant, also glue application throughout the entire surface is extremely important for defect-free product packaging boxes . Normal equipment upkeep and extensive calibration are vital preventative actions.
Optimizing Adhesive Volume and Protection
The complete amount of glue applied throughout the setting up of product packaging boxes is as crucial as its even circulation. Inadequate sticky quantity leads to insufficient wetting of the substrates. The adhesive film has to be significant enough to cover the whole bonding location effectively. If the applied adhesive layer is also thin, it can not effectively pass through the paperboard’s tiny fibers or the face product. This failing to penetrate lead to a shallow, weak bond. The adhesive may not create a constant, unbroken movie securing the plies of the packaging boxes with each other. In such situations, even small stress and anxieties from taking care of, shipping, or ecological modifications can trigger delamination. These delaminated locations look like unwanted bubbles on the finished packaging boxes . Suppliers must perform trials to figure out and maintain optimum glue grammage, or layer weight. This spec is distinct to every product and glue mix utilized for their packaging boxes . This method ensures appropriate bond strength and protects against bubble formation.
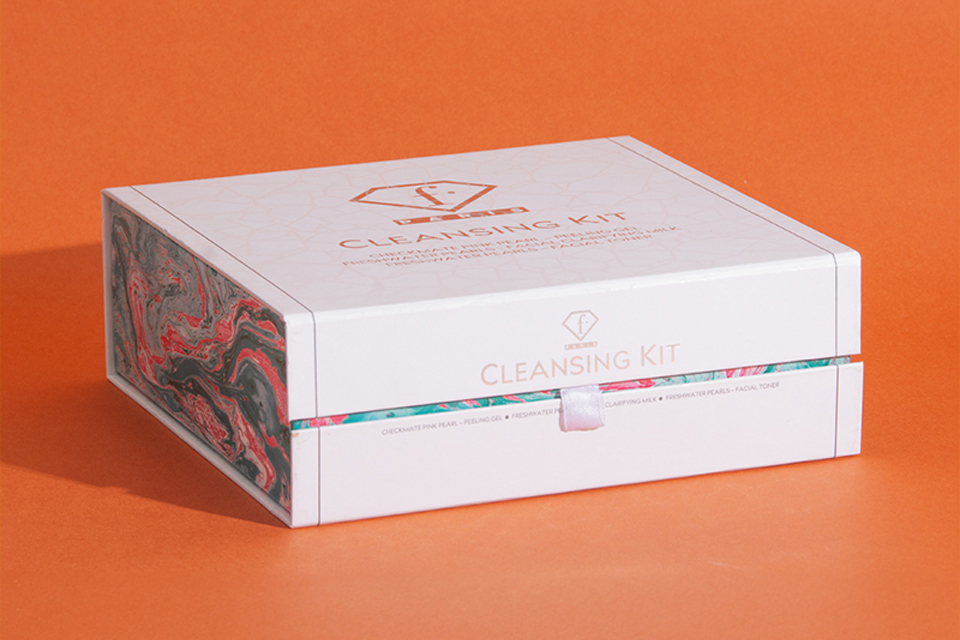
Thermal Administration in Adhesive Systems
Numerous advanced adhesive systems used in making modern-day packaging boxes , particularly hot-melt adhesives, need exact thermal control. THese industrial adhesives have to constantly get to and keep a details operating temperature array. This ensures htey attain their designed thickness adn ideal circulation attributes during application. If the adhesive is not heated sufficiently in the melting tank, transfer pipes, or applicator heads, it will certainly not melt entirely or attain consistent uniformity. This oversight in thermal administration causes several troubles throughout application. Unmelted or partially dissolved sticky bits can develop disruptive clumps or touches in the used adhesive line. This causes an irregular glue application on the packaging boxes . Seriously, the adhesive’s capability to correctly wet out surface areas adn pass through the materials’ fibrous structure is endangered. Consequently, poor adhesion takes place in localized areas. Bubbles can after that quickly create where the bond is naturally weak, discontinuous, or non-existent. Preserving proper, steady temperature throughout the adhesive delivery system is essential for producing consistent, top quality packaging boxes .
Substratum Compatibility and Surface Area Energy Characteristics
The interaction at the interface in between sticky and substrate surfaces profoundly affects bond top quality in packaging boxes . Various materials made use of in product packaging, like different paperboard qualities, covered stocks, or laminated movies, possess unique surface powers. Adhesives have to be meticulously picked or created to effectively “damp out” these details surface areas. “Moistening out” explains an adhesive’s capability to spread out uniformly across a solid surface, rather than beading. If a substratum’s surface area power is also low, typical with specific polymer finishings or plasticized papers in costs product packaging boxes , the sticky might grain up. It fails to spread out right into the desired continual film. This beading creates locations with insufficient glue protection. These poorly bound areas come to be prime locations for bubble development. Selecting an adhesive compatible with the surface area attributes of all selected products is fundamental for strong, dependable bonds in product packaging boxes . In some specialized applications, surface area treatments like corona discharge customize low-energy substrates. These treatments enhance glue receptivity but include procedure intricacy and expense to packaging boxes manufacturing.
The Influence of Entrapped Air and Lamination Parameters
The physical dynamics of the lamination procedure itself can accidentally present defects like bubbles right into product packaging boxes . During the signing up with stage, ambient air can come to be physically entraped between the main substrate and the face material. This concern is prevalent if lamination equipment is not thoroughly adjusted or if operating criteria are not enhanced for the specific materials and adhesive. Secret connecting variables consist of maker speed and pressure applied by laminating flooring rollers. If the maker operates at extreme speed about the adhesive’s open time or establishing speed, there may want time for air to get away prior to the bond collections. Similarly, if roller pressure is as well reduced, it may not properly eject all entrapped air from the nip point. This caught air, especially if packaging boxes are later revealed to raised temperature levels or if materials outgas, can increase. The broadening air applies pressure, requiring layers apart and developing noticeable bubbles. These bubbles concession both aesthetics and structural integrity of the packaging boxes . Cautious control of lamination parameters is essential to minimize this typical danger.

Conclusion
In recap, a mix of distinctive aspects contributes to the undesirable development of bubbles on packaging boxes . These reasons consist of too much ecological dampness in basic materials and imprecise sticky application due to maker miscalibration. Inadequate adhesive quantity or improper thermal management of the sticky system also play critical roles. In addition, challenges with substrate compatibility, surface area energy distinctions, and physical air entrapment throughout lamination can cause these flaws in product packaging boxes . Manufacturing companies can properly stop bubbling by comprehending these underlying scientific and technological principles. Executing rigorous, multi-stage quality control measures at each production point for product packaging boxes is essential. Maintaining visual appeal and guaranteeing structural honesty are paramount for upholding product top quality understanding. This, consequently, safeguards brand name track rocord and fosters customer confidence in an affordable worldwide market.