Exact Box Dimension for Ideal Product Bundle Fit
Introduction
Exact measurement develops the bedrock of effective product packaging logistics. When services or individuals prepare products for shipment or storage space, the accuracy with which they Determine a Box straight influences product security, expense performance, and total operational success. An appropriately sized item bundle decreases the risk of damages throughout transportation. It additionally optimizes material use and decreases shipping expenditures. This overview gives an organized, technological explanation for measuring various box and item kinds. It ensures your things get the optimum unit.
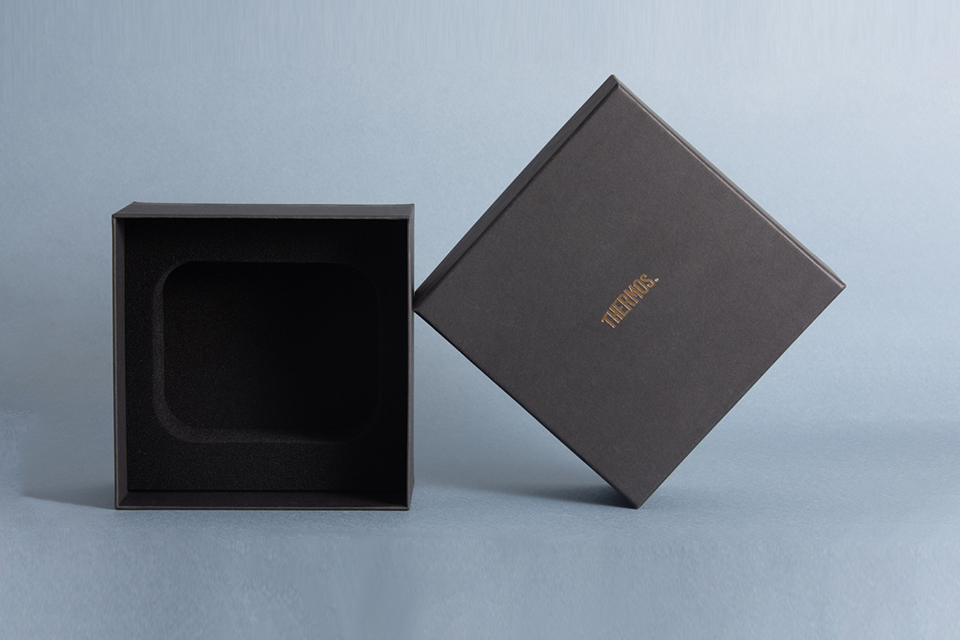
1. Vital Toolkit for Specific Box Dimension
Accurate dimensional evaluation requires appropriate instrumentation. Before initiating the process to Measure a Box, set up the following devices:
Determining Tool (Ruler or Measuring Tape): An adjusted leader or a retracting measuring tape supplies the primary methods of dimensioning. Ensure the tool shows clear, exact markings in your called for systems (inches or centimeters). For larger boxes, a measuring tape uses greater comfort. Steel leaders typically provide premium rigidness for straight-line measurements. Straight Side (Optional yet Recommended): A rigid straight edge, such as a steel ruler or a tough item of flat product, aids in achieving real linear dimensions. It confirms particularly valuable when measuring throughout uneven surfaces or ensuring alignment. Package for Measurement: The target box must be completely put together. If it is a flat-packed box, construct it into its last three-dimensional kind before proceeding.
2. Determining Common Box Capacities: Length, Size, Height
The fundamental external dimensions of any kind of rectangle-shaped or square product plan consist of its length, size, and elevation. Sector convention determines a specific order and alignment for these measurements:
Size (L): Determine the lengthiest panel of the assembled box when checked out from its opening. Step this measurement from one side to the opposing side. Maintain the determining tool alongside this edge. Width (W): Next, identify the much shorter panel adjacent to the size. Procedure this dimension across. This is generally the panel perpendicular to the length. Elevation (H)/ Depth (D): This dimension represents the dimension from the base of package to its leading opening. Alternatively, if the box is pushing its side, it is the measurement vertical to both the size and size planes. Constantly put package on a flat, stable surface area throughout dimension. Tape-record each dimension immediately to avoid mistakes. For consistency, constantly Determine a Box on the surface unless internal measurements are specifically called for.
3. Accountancy for Box Flaps and Building And Construction
When you Measure a Box, specifically a conventional slotted carton (RSC), ensure you gauge the main body. Do not include the flaps in the key elevation dimension if they expand past the primary box structure when open. Come up to ball game lines where the flaps fold to satisfy the box. If the flaps overlap or satisfy in the center, this does not alter the primary exterior elevation of the box’s main compartment. Comprehending box building and construction aids in determining the proper factors for dimension.
4. The Criticality of Internal Box Capacities
While exterior dimensions are vital for delivery and storage space thickness calculations, the interior measurements dictate the functional area for your item. To determine the interior dimensions of a product plan:
Action tjhe size, size, and and height from the inside surface areas of the box. Additionally, if direct interior measurement is challenging, determine the density of the corrugated material (package wall surface). Deduct two times the product thickness from each external measurement (e.g., Inner Size = Exterior Size – 2 * Wall Surface Thickness). Precise interior measurements are vital. They ensure your item fits well, with appropriate area for safety packaging materials like bubble cover or foam inserts. This protects against motion and potential damage.
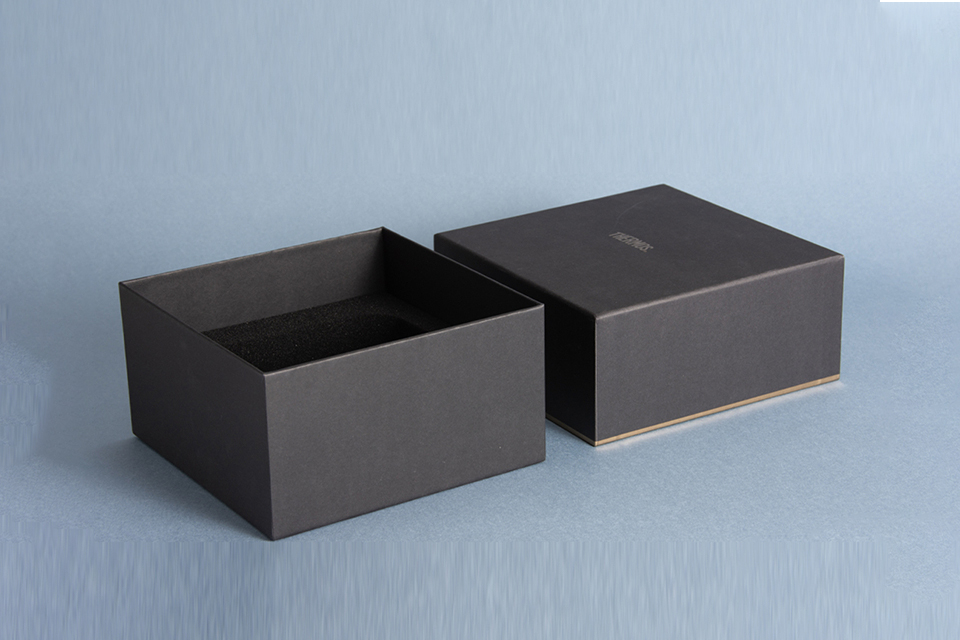
5. Confirmation: The Double-Check Imperative
Accuracy is critical. After tape-recording the preliminary set of dimensions, perform a verification check. Remeasure each dimension (Length, Size, Elevation) at the very least as soon as. Small disparities can cause significant issues. These consist of inaccurate delivery fee computations, wasted products, or items that do not fit the intended item package. This easy re-verification step minimizes costly errors.
6. Determining Dimensional Weight: A Key Factor
Shipping carriers like FedEx, UPS, and DHL frequently utilize a pricing technique called dimensional (DIM) weight. This technique takes into consideration the amount of area an item bundle occupies in connection with its actual weight. Carriers calculate DIM weight making use of a formula, generally: (Length x Size x Height)/ DIM Divisor. The DIM Divisor is a number established by the service provider. They then charge for the higher of the actual weight or the DIM weight.
As a result, specific exterior dimensions when you Gauge a Box are financially important. Even a little overestimation in measurements can pump up the calculated DIM weight. This results in suddenly greater shipping costs. Conversely, underestimation could cause billing modifications and hold-ups. Comprehending and properly computing potential DIM weight permits much better price administration in your packaging and delivery strategy.
7. Measuring Round Products for Appropriate Product Packaging
To successfully Measure a Box or select appropriate packaging for a round item, you must identify two main measurements of the product itself:
Diameter (or Circumference): Determine the widest part of the cyndrical tube. If determining diameter directly, discover the straight line distance across the circular base, travelling through its center. If measuring area, wrap a versatile measuring tape comfortably around the widest component. You can compute the diameter from the area making use of the formula: Size = Circumference/ π (where π ≈ 3.14159). Height (H): Measure the product’s elevation from its base to its top along its central axis. Make use of a ruler or measuring tape, ensuring it stays perpendicular to the base. When selecting a box, ensure its interior dimensions suit the cyndrical tube’s diameter (or size and length slightly larger than size) and its elevation, plus any kind of padding.
8. Determining Rectangular Products for Optimal Box Sizing
For rectangular or cuboid items, the dimension procedure mirrors that of a box. Identify and determine three essential measurements of the product:
Item Length: The longest side of the item. Product Width: The much shorter side, perpendicular to the length Product Height/Depth: The dimension perpendicular to both length and width. Use a leader or measuring tape. For optimal product package fit, include a little allocation to every dimension (e.g., 2mm to 5mm, or 0.08 to 0.2 inches) when picking or designing a box. This “resistance” provides area for very easy insertion and elimination, and for minimal protective wrap if needed, without the fit being as well loose.
9. Methodology for Measuring Round Boxes (Cylinders/Tubes)
Round boxes, frequently referred to as cylinder boxes or tubes, possess one-of-a-kind geometry. Their lids and bottoms are round and normally of the same size. This simplifies the procedure to Determine a Box of this type:.
Diameter (D): Measure the straight-line distance across the level round top or base, passing through the center. You just require to measure this as soon as. Height (H): Measure the range from the base of the round box to its leading edge, vertical to the circular base. The key measurements for a round product bundle are its diameter and elevation. These establish its capacity and the area it will certainly inhabit.
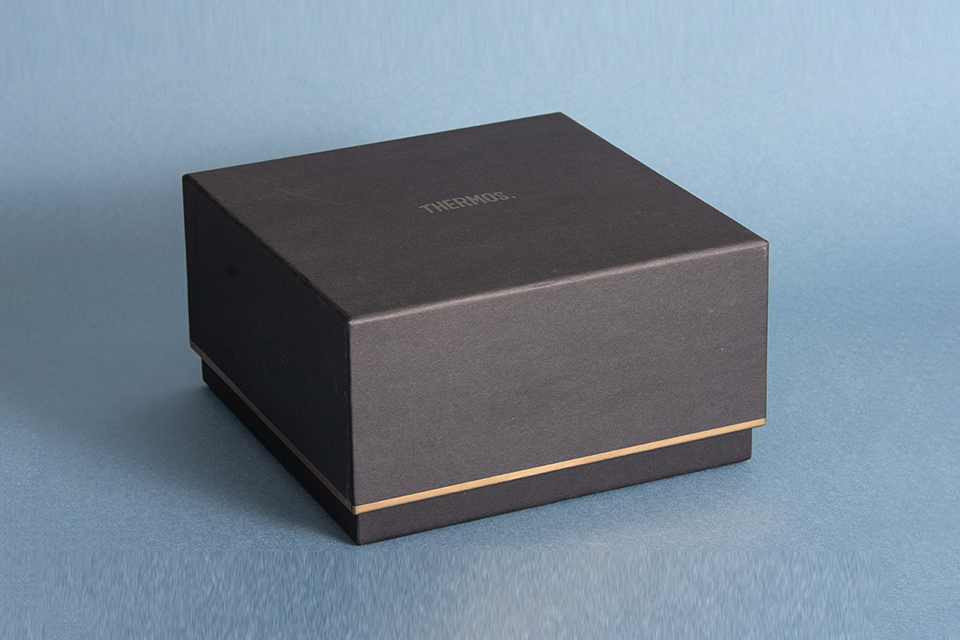
Conclusion
Mastering the strategy to properly Determine a Box and the products it will consist of is a fundamental ability in reliable product packaging and logistics. Accurate measurements make sure item safety, control shipping costs influenced by dimensional weight, and optimize material usage. By regularly using the organized techniques detailed for numerous forms, companies and people can with confidence select or design the ideal item bundle. This interest to detail underpins successful delivery, storage space, and overall customer complete satisfaction. Specialist examination can even more improve complicated product packaging requirements.